By niuelec | 15 May 2025 | 0 Comments
The Vital Role of Eco-Friendly Bimetallic Lugs in Renewable Energy
The global shift towards renewable energy sources like solar, wind, and hydro power is more than a trend; it's a fundamental transformation of our energy landscape. As nations strive to meet ambitious climate goals and reduce carbon footprints, the development and deployment of green power infrastructure are accelerating at an unprecedented pace. While solar panels, wind turbines, and advanced battery storage systems often take center stage, the silent, often unseen components within these systems are equally critical to their success, efficiency, and long-term sustainability. Among these unsung heroes are electrical connectors, specifically eco-friendly bimetallic lugs supplied by trusted bimetallic lugs suppliers, which ensure the seamless and reliable flow of green electricity. Their importance cannot be overstated, as they form the critical links in the energy chain, directly impacting system performance, safety, and environmental integrity.
Table of contents:
The Linchpin of Renewable Systems: Ensuring Stability and Integrity
Green Manufacturing: Friction Welding Versus The Old Guard in Connector Production
Boosting Efficiency, Slashing Energy Waste Through Superior Connections
Versatility Across the Spectrum of Green Infrastructure Applications
Durability for a Sustainable Future: Longevity and Reduced Waste
A subpar connection, however, can be a significant point of failure. Poor contact can lead to increased electrical resistance, resulting in substantial energy losses that diminish the overall output of the renewable energy system. More critically, high resistance generates excess heat. This thermal stress not in itself an energy loss, can degrade insulation, accelerate material fatigue, and, in worst-case scenarios, lead to catastrophic failures such as electrical fires. Such incidents not only compromise the safety and operational lifespan of the installation but also undermine the economic viability and public trust in green energy projects.
Many renewable energy systems also present a unique material challenge: the need to connect aluminum conductors, often used for their lighter weight and cost-effectiveness in large-scale cabling, with copper components prevalent in switchgear and equipment terminals. Direct connection of these dissimilar metals can lead to galvanic corrosion, a process that degrades the connection over time, increasing resistance and risk. This is where bimetallic lugs become indispensable. These specialized connectors, typically featuring a copper palm and an aluminum barrel, are designed to create a stable and durable transition between copper and aluminum conductors. By preventing direct contact between the two metals at the termination point, they mitigate the risk of corrosion, ensuring a reliable, low-resistance connection that upholds the integrity and efficiency of the entire green power system.
In stark contrast, friction welding stands out as a significantly more environmentally benign manufacturing process for producing bimetallic lugs. Friction welding is a solid-state joining process that generates heat through mechanical friction between a rotating workpiece and a stationary one. When the interface reaches a suitable temperature, the parts are forged together under pressure, creating a true metallurgical bond without melting the parent materials. This method offers several key environmental advantages. Firstly, it eliminates the need for filler metals, fluxes, or protective gases, thereby reducing material consumption and waste. Crucially, the process is clean – it produces no smoke, fumes, or slag. Unlike electroplating or chemical treatments, friction welding does not involve hazardous substances like acids or heavy metals, thus circumventing the generation of toxic wastewater or chemical residues.
This makes friction-welded bimetallic lugs inherently more aligned with the ethos of green energy. Components manufactured using such cleaner technologies are increasingly sought after for low-carbon projects and can more easily integrate into sustainable supply chains. As the scrutiny on the embodied carbon and environmental impact of all components in green infrastructure intensifies, the choice of manufacturing process for even the smallest parts, like cable lugs, becomes a significant factor.
Contact resistance is an inherent property of any electrical connection, but it can be exacerbated by poor design, improper installation, or material degradation. When current flows through a connection with high resistance, a portion of the electrical energy is converted into heat. This dissipated heat represents a direct loss of valuable green energy that could otherwise be fed into the grid or used to power homes and businesses. Over the lifetime of a renewable energy installation, even seemingly small losses at numerous connection points can accumulate into a substantial waste of energy and revenue.
Bimetallic lugs engineered with precision, particularly those utilizing advanced joining techniques like friction welding, offer superior electrical conductivity and mechanical integrity at the critical copper-aluminum interface. The solid-state metallurgical bond created by friction welding ensures a low-resistance pathway for current, significantly reducing the likelihood of resistive heating. This not only conserves energy but also enhances the operational stability and longevity of connected equipment. For example, in a solar power system, efficient connections to the inverter are crucial for maximizing the conversion of DC power from the panels to AC power for the grid. Reduced heat generation at lug terminations also means less thermal stress on surrounding components, contributing to a cooler operating environment and potentially extending the lifespan of sensitive electronics. By choosing bimetallic lugs designed for optimal energy transfer, project developers can tangibly improve the overall conversion efficiency and energy yield of their renewable power systems.
Their inherent ability to bridge copper and aluminum conductors makes them indispensable in scenarios where different conductor materials are employed for reasons of cost, weight, or current-carrying capacity. For instance, large wind farms might use substantial aluminum cables for power transmission from turbines to substations, where they connect to copper-based switchgear. Solar installations often feature aluminum wiring in combiner boxes and arrays connecting to copper components in inverters. Energy storage systems and EV charging infrastructure also rely on high-current connections where the flexibility of bimetallic solutions is advantageous.
To cater to this wide range of applications, bimetallic lugs are available in many different cable lugs types. This includes a broad spectrum of sizes to accommodate various cable cross-sections, from smaller gauge wires to large power cables. Furthermore, they come with different palm hole diameters and configurations (e.g., single-hole, double-hole) to ensure secure and appropriate connections to different types and sizes of equipment terminals and busbars. This versatility in cable lugs types allows system designers and installers to select the optimal connector for each specific application, ensuring both electrical integrity and mechanical security. The straightforward design of most bimetallic lugs also facilitates relatively quick and easy installation and maintenance, which is a crucial factor in reducing on-site labor time and associated costs, especially for large-scale projects.
The copper-aluminum interface is particularly vulnerable to corrosion if not properly managed. Moisture and pollutants can accelerate galvanic corrosion if metals are in direct contact or the joint is weak. Friction welding creates a strong, void-free bond at the atomic level between copper and aluminum, highly resistant to oxidation and corrosion, even in harsh conditions like coastal or industrial areas.
High-quality bimetallic lugs lower the risk of degradation at connection points, reducing maintenance and replacements. Fewer replacements mean less raw material use, energy consumption, and waste. This improves overall sustainability and lowers lifecycle costs for renewable energy projects. Reliable connections also boost system uptime for continuous power generation. For especially harsh environments, bimetallic lugs can be further protected with insulating shrouds or sealed encapsulation, extending their lifespan and ensuring long-term infrastructure integrity.
In conclusion, while the turbines spin and panels absorb sunlight, the humble bimetallic lug works tirelessly to ensure that the green energy generated is delivered efficiently and reliably. Their role in bridging dissimilar metals, their contribution to system efficiency through low-resistance connections, their adaptability to diverse applications, and their long-term durability make them indispensable components. Moreover, when produced using environmentally conscious methods like friction welding, they align perfectly with the sustainable ethos of the renewable energy sector. As the demand for green power continues to grow, the selection of high-quality, eco-friendly connectors will remain a critical factor in building a truly sustainable energy future. For project developers and engineers looking to optimize their renewable energy systems, partnering with specialized cable lug manufacturers is key. Companies such as Niuelec, a prominent bimetallic lugs supplier, demonstrate a strong commitment to this vision by focusing on advanced friction welding techniques for their bimetallic components, ensuring that even the smallest parts contribute significantly to a larger, greener, and more efficient energy world.
Table of contents:
The Linchpin of Renewable Systems: Ensuring Stability and Integrity
Green Manufacturing: Friction Welding Versus The Old Guard in Connector Production
Boosting Efficiency, Slashing Energy Waste Through Superior Connections
Versatility Across the Spectrum of Green Infrastructure Applications
Durability for a Sustainable Future: Longevity and Reduced Waste
The Linchpin of Renewable Systems: Ensuring Stability and Integrity
In any electrical system, connectors are the nodal points that guarantee the continuity and stability of power transmission. This role becomes even more pronounced in renewable energy installations such as sprawling solar farms or towering wind turbines. These systems generate substantial amounts of electricity that must be efficiently collected, converted, and transmitted. Cable lugs, though seemingly small components, are fundamental to this process. They provide secure termination points for electrical cables, connecting them to busbars, circuit breakers, inverters, and other vital equipment.A subpar connection, however, can be a significant point of failure. Poor contact can lead to increased electrical resistance, resulting in substantial energy losses that diminish the overall output of the renewable energy system. More critically, high resistance generates excess heat. This thermal stress not in itself an energy loss, can degrade insulation, accelerate material fatigue, and, in worst-case scenarios, lead to catastrophic failures such as electrical fires. Such incidents not only compromise the safety and operational lifespan of the installation but also undermine the economic viability and public trust in green energy projects.
Many renewable energy systems also present a unique material challenge: the need to connect aluminum conductors, often used for their lighter weight and cost-effectiveness in large-scale cabling, with copper components prevalent in switchgear and equipment terminals. Direct connection of these dissimilar metals can lead to galvanic corrosion, a process that degrades the connection over time, increasing resistance and risk. This is where bimetallic lugs become indispensable. These specialized connectors, typically featuring a copper palm and an aluminum barrel, are designed to create a stable and durable transition between copper and aluminum conductors. By preventing direct contact between the two metals at the termination point, they mitigate the risk of corrosion, ensuring a reliable, low-resistance connection that upholds the integrity and efficiency of the entire green power system.
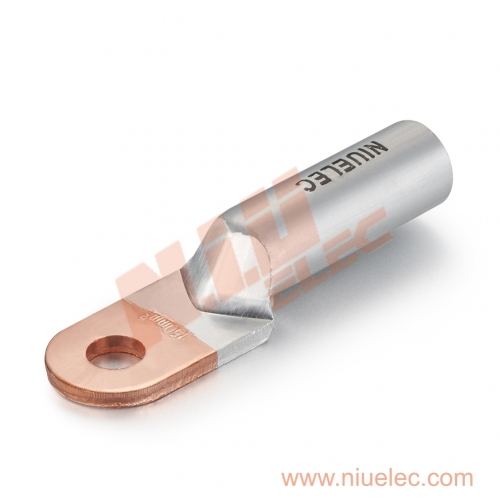
Green Manufacturing: Friction Welding Versus The Old Guard in Connector Production
The environmental credentials of a renewable energy project extend beyond its operational phase; they encompass the entire lifecycle, including the manufacturing processes of its components. For electrical connectors like bimetallic lugs, the production method significantly influences their eco-friendliness. Traditional manufacturing techniques for bimetallic connections, such as explosive welding, casting, or certain types of pressure welding followed by electroplating, often involve processes with considerable environmental footprints. For instance, casting can be energy-intensive, while electroplating processes used to enhance corrosion resistance or conductivity often rely on hazardous chemicals, including heavy metals and acidic solutions, generating significant volumes_of chemical wastewater that requires extensive and costly treatment. Acid pickling, another common step to prepare metal surfaces, also produces harmful waste.In stark contrast, friction welding stands out as a significantly more environmentally benign manufacturing process for producing bimetallic lugs. Friction welding is a solid-state joining process that generates heat through mechanical friction between a rotating workpiece and a stationary one. When the interface reaches a suitable temperature, the parts are forged together under pressure, creating a true metallurgical bond without melting the parent materials. This method offers several key environmental advantages. Firstly, it eliminates the need for filler metals, fluxes, or protective gases, thereby reducing material consumption and waste. Crucially, the process is clean – it produces no smoke, fumes, or slag. Unlike electroplating or chemical treatments, friction welding does not involve hazardous substances like acids or heavy metals, thus circumventing the generation of toxic wastewater or chemical residues.
This makes friction-welded bimetallic lugs inherently more aligned with the ethos of green energy. Components manufactured using such cleaner technologies are increasingly sought after for low-carbon projects and can more easily integrate into sustainable supply chains. As the scrutiny on the embodied carbon and environmental impact of all components in green infrastructure intensifies, the choice of manufacturing process for even the smallest parts, like cable lugs, becomes a significant factor.
Boosting Efficiency, Slashing Energy Waste Through Superior Connections
The primary function of any electrical connector is to transmit power with minimal loss. In the context of renewable energy, where maximizing output and efficiency is paramount, the quality of these connections directly impacts the system's overall performance and return on investment. High-quality bimetallic lugs contribute significantly to reducing energy losses by minimizing contact resistance at termination points.Contact resistance is an inherent property of any electrical connection, but it can be exacerbated by poor design, improper installation, or material degradation. When current flows through a connection with high resistance, a portion of the electrical energy is converted into heat. This dissipated heat represents a direct loss of valuable green energy that could otherwise be fed into the grid or used to power homes and businesses. Over the lifetime of a renewable energy installation, even seemingly small losses at numerous connection points can accumulate into a substantial waste of energy and revenue.
Bimetallic lugs engineered with precision, particularly those utilizing advanced joining techniques like friction welding, offer superior electrical conductivity and mechanical integrity at the critical copper-aluminum interface. The solid-state metallurgical bond created by friction welding ensures a low-resistance pathway for current, significantly reducing the likelihood of resistive heating. This not only conserves energy but also enhances the operational stability and longevity of connected equipment. For example, in a solar power system, efficient connections to the inverter are crucial for maximizing the conversion of DC power from the panels to AC power for the grid. Reduced heat generation at lug terminations also means less thermal stress on surrounding components, contributing to a cooler operating environment and potentially extending the lifespan of sensitive electronics. By choosing bimetallic lugs designed for optimal energy transfer, project developers can tangibly improve the overall conversion efficiency and energy yield of their renewable power systems.
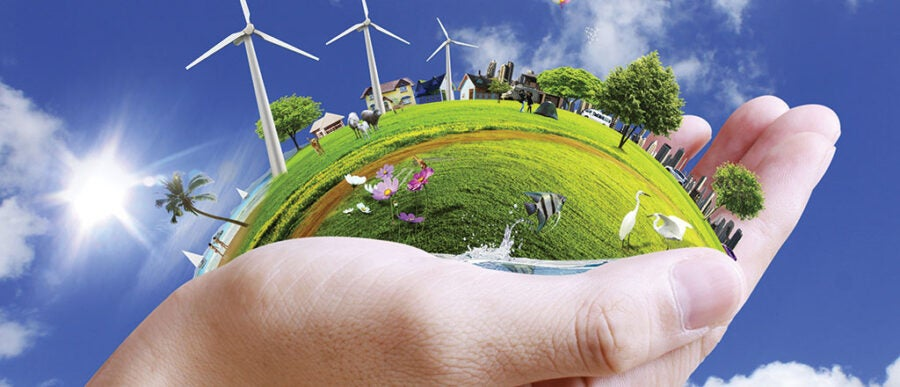
Versatility Across the Spectrum of Green Infrastructure Applications
The green energy revolution encompasses a diverse array of technologies and infrastructure projects, each with its unique set of electrical connection requirements. From the nacelles of wind turbines buffeted by strong winds to expansive solar arrays baking under the sun, and from sophisticated battery energy storage systems (BESS) to the rapidly expanding network of electric vehicle (EV) charging stations, the need for reliable and robust electrical connectors is universal. Bimetallic lugs are particularly well-suited to meet these varied demands.Their inherent ability to bridge copper and aluminum conductors makes them indispensable in scenarios where different conductor materials are employed for reasons of cost, weight, or current-carrying capacity. For instance, large wind farms might use substantial aluminum cables for power transmission from turbines to substations, where they connect to copper-based switchgear. Solar installations often feature aluminum wiring in combiner boxes and arrays connecting to copper components in inverters. Energy storage systems and EV charging infrastructure also rely on high-current connections where the flexibility of bimetallic solutions is advantageous.
To cater to this wide range of applications, bimetallic lugs are available in many different cable lugs types. This includes a broad spectrum of sizes to accommodate various cable cross-sections, from smaller gauge wires to large power cables. Furthermore, they come with different palm hole diameters and configurations (e.g., single-hole, double-hole) to ensure secure and appropriate connections to different types and sizes of equipment terminals and busbars. This versatility in cable lugs types allows system designers and installers to select the optimal connector for each specific application, ensuring both electrical integrity and mechanical security. The straightforward design of most bimetallic lugs also facilitates relatively quick and easy installation and maintenance, which is a crucial factor in reducing on-site labor time and associated costs, especially for large-scale projects.
Durability for a Sustainable Future: Longevity and Reduced Waste
Sustainability in green energy projects isn’t just about clean power—it’s also about durable infrastructure that minimizes replacements, reducing resource use and waste. Electrical connectors play a crucial role in this vision. Bimetallic lugs, especially those made with techniques like friction welding, offer superior durability and corrosion resistance, ensuring longer lifespans and fewer maintenance cycles.The copper-aluminum interface is particularly vulnerable to corrosion if not properly managed. Moisture and pollutants can accelerate galvanic corrosion if metals are in direct contact or the joint is weak. Friction welding creates a strong, void-free bond at the atomic level between copper and aluminum, highly resistant to oxidation and corrosion, even in harsh conditions like coastal or industrial areas.
High-quality bimetallic lugs lower the risk of degradation at connection points, reducing maintenance and replacements. Fewer replacements mean less raw material use, energy consumption, and waste. This improves overall sustainability and lowers lifecycle costs for renewable energy projects. Reliable connections also boost system uptime for continuous power generation. For especially harsh environments, bimetallic lugs can be further protected with insulating shrouds or sealed encapsulation, extending their lifespan and ensuring long-term infrastructure integrity.
In conclusion, while the turbines spin and panels absorb sunlight, the humble bimetallic lug works tirelessly to ensure that the green energy generated is delivered efficiently and reliably. Their role in bridging dissimilar metals, their contribution to system efficiency through low-resistance connections, their adaptability to diverse applications, and their long-term durability make them indispensable components. Moreover, when produced using environmentally conscious methods like friction welding, they align perfectly with the sustainable ethos of the renewable energy sector. As the demand for green power continues to grow, the selection of high-quality, eco-friendly connectors will remain a critical factor in building a truly sustainable energy future. For project developers and engineers looking to optimize their renewable energy systems, partnering with specialized cable lug manufacturers is key. Companies such as Niuelec, a prominent bimetallic lugs supplier, demonstrate a strong commitment to this vision by focusing on advanced friction welding techniques for their bimetallic components, ensuring that even the smallest parts contribute significantly to a larger, greener, and more efficient energy world.
Leave a Reply
Your email address will not be published.Required fields are marked. *
CATEGORIES